Optimizing Combined Cycle Power Plant Operations
Credit to Author: Contributed Content| Date: Mon, 03 Apr 2023 04:08:00 +0000
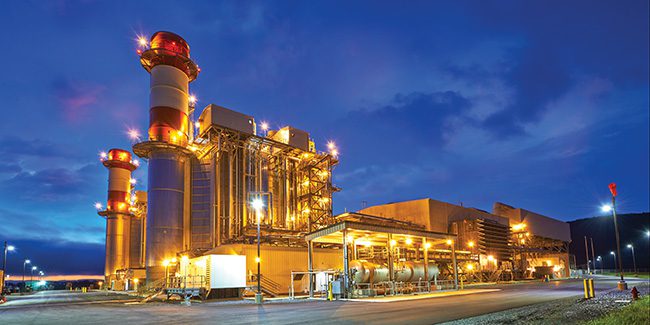
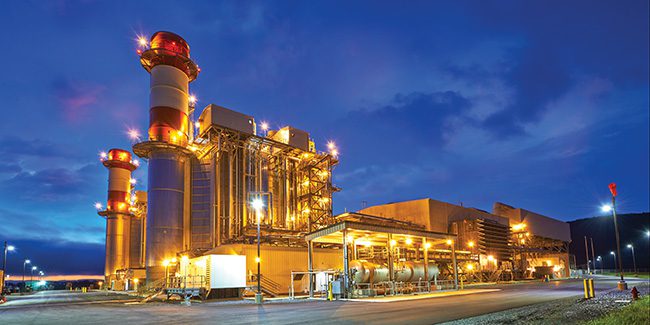
Cogentrix Energy and Siemens Energy have partnered to optimize 8000H-class gas turbine reliability and outage planning. Under Cogentrix’s management, the Patriot site successfully upgraded one of its combustion turbine rotors in 2021, and the Liberty plant achieved a continuous operations record for H-class 60-Hz machines at 206 days.
Patriot and Liberty (together known as the “Hamilton” portfolio) are two natural gas–fired combined cycle projects in Pennsylvania. Both projects utilize Siemens Energy’s world-class 8000H technology and started commercial operations in 2016. Cogentrix took over management of the facilities from previous owners in June 2020, and the operational performance of both plants has improved significantly since that time.
Cogentrix is a private independent power producer that provides best-in-class technical, operational, financial, and commercial capabilities. Cogentrix has 40 years of experience operating combined cycle gas turbine (CCGT) power plants, including many equipped with Siemens Energy’s technology. Today, Cogentrix operates a diverse fleet of natural gas-fired projects with more than 9 GW of capacity spread across the PJM Interconnection, ISO-New England, Electric Reliability Council of Texas (ERCOT), and SERC Reliability Corporation markets.
Cogentrix operational excellence is exemplified by its CCGT fleet’s low Equivalent Forced Outage Rate – demand (EFORd) figures of 0.52% in 2020 and 1.01% in 2021, which compare favorably with the North American Electric Reliability Corporation (NERC) averages of 4.26% and 5.07% in the same periods. In 2022, Patriot and Liberty had a combined EFORd of less than 0.4%, representing the best year of operations under Cogentrix management.
Plant Designs
The Patriot (shown above) and Liberty plants each consist of two units, each a single-shaft clutched configuration, two Siemens Energy SGT6-8000H combustion turbines (CTs) with dry-low-NOx combustors and evaporative coolers. Each combustion and steam turbine combination is connected to a 462-MVA, 23-kV generator equipped with a static excitation system. The steam turbine generators are two Siemens Energy SST6-5000 tandem-compound reheat type with cooling provided by air-cooled condensers. The heat recovery steam generators are two Vogt, three-pressure-level with superheat and reheat systems, and supplemental duct firing capabilities.
Both plants utilize 100% reverse osmosis/electro-deionization trains with ultrafiltration (UF) pre-filters and chemical treatment. The water treatment systems at both plants include a 635,000-gallon storage tank for feedwater and the fire systems. Wastewater systems at both plants are served by the local municipal system.
Emergency diesel generators (EDGs) are 1,000 kW connected to two essential services motor control centers. The Siemens Energy SGT6-8000H turbines short startup times, low heat rate, and high operational flexibility help achieve long and sustained run-times. In fact, Cogentrix was able to achieve a 206-consecutive-day run time record at Liberty, which is considered the longest of a Siemens Energy SGT6-8000H unit. Modern blade design and optimized packaging promote high reliability while keeping operations and maintenance (O&M) costs and outage risk low.
Operational Improvements
Cogentrix has a very strong relationship with Siemens Energy, which manufactured the SGT6-8000H units and provides maintenance services under long-term service agreements (LTSAs). Together, Cogentrix and Siemens Energy were able to reduce ongoing maintenance costs while incorporating financially beneficial performance upgrades for the gas turbines, including planned rotor upgrades at both Liberty and Patriot.
Cogentrix has a strong track record of improving plant performance and embedding a reliability-focused maintenance philosophy to ensure sustained performance. As previously mentioned, the company took over operations of Hamilton in June 2020. Prior to Cogentrix assuming operations, the facilities had struggled to implement technical advancements/enhancements for power and reliability. When Cogentrix stepped in, it was able to collaborate with Siemens Energy and other original equipment manufacturers to modernize the facilities.
![]() |
1. Ten members of the current Patriot plant team, including General Manager Sean Davis (far right), are standing near the units. Courtesy: Cogentrix Energy |
Cogentrix utilizes an operations model developed from industry best practices to perform an overall plant operations management assessment. This was completed by September 2020 and the team implemented short-term changes to staff and responsibilities (Figures 1 and 2). In late fall 2020 and into 2021, the team had a very busy outage season across the four turbines, which involved three hot-gas-path inspections, one unit upgrade that included a CT rotor exchange for outage duration efficiency, and steam turbine and steam turbine generator inspections.
![]() |
2. Twelve members of the current Liberty plant team, including General Manager Brian Zechman (front row, third from the left), are standing near the units. Courtesy: Cogentrix Energy |
Operational Excellence with Focus on Safety and Training
Initially, the Hamilton project’s operations team experienced operational bumps in the road and did not use the experiences at both facilities to grow. After Cogentrix stepped in as O&M and asset manager, the Cogentrix fleetwide operations model was utilized to improve human error prevention and reliability. The sites implemented human error prevention training, work management and process implementation, budget development, and an environmental stewardship program.
Operating procedures were in place prior to Cogentrix, but did not take advantage of lessons learned between the two facilities that are identical and located in close proximity to one another. Areas that differed between the facilities included: emissions response, steam turbine heat up from cold start, and identified key plant parameters.
Cogentrix partnered with a human performance improvement specialist to provide Human Performance Initiative training to all personnel in leadership positions. The process includes utilization of error trap identification techniques and tools to mitigate human performance errors. The training was recorded, and then the initiative was implemented across the fleet at all levels in the plant. Human performance improvement tools have been integrated into each activity and use of these tools brings critical thinking and a broader perspective into everything Cogentrix personnel do.
The development of the Hamilton operations model and code of conduct has added a great deal of value to the qualification and training process for all levels of the operations team. These two programs and the work of the operations managers has improved consistency across the two plants and opened communications between the operations teams.
The qualification program at both facilities initially relied heavily on Siemens Energy and vendor training provided during the construction and commissioning of the facilities. Staff turnover and promotions required this thought process to be challenged and improved to include formal qualification processes for each of the three operations roles in addition to Siemens Energy training. All operations personnel were required to retrain up to their current position and complete any upgrades that may have been overlooked by the original process.
This model of training has and will ensure that both facilities maintain a highly functional, dynamic operations team. The operations qualification process concept has begun to grow to include potential training for the maintenance team as well. Previously, maintenance personnel were limited to attending vendor specific training or occasional in-house training but rarely anything that developed the more advanced skills a plant of this technology required. Additional planning is taking shape for the mechanical and ICE (instrumentation, controls, and electrical) training program that will broaden the capabilities of these employees and the Hamilton maintenance group as a whole, including specialized training on the latest technology.
Both facilities continue to use employee driven safety committees to identify, document, and address safety concerns. Safety ideas and improvements can be shared more freely under the new Hamilton portfolio format and the EHS (environmental, health, and safety) manager conducts cross facility safety meetings with key employees to help foster this practice. A centralized Cogentrix “Observation” database provides a tool to look for behavior/site indicators that enable safety incidents. Site housekeeping standards have been improved and Cogentrix leadership provided a new perspective on the importance of properly maintaining the facilities and how that translates into the Cogentrix safety culture.
Building a Collaborative Culture and Improving Outage Performance
When Cogentrix took over control of the facilities, they were renamed Hamilton Patriot and Hamilton Liberty. This was the first step toward creating a collaborative culture among both facilities that was missing. Since then, Cogentrix has actively sought to encourage teamwork between the sister facilities, which has yielded great results.
The operations managers from both Hamilton facilities developed a comprehensive support structure that fostered the exchange of information between the plants and coordinated the training process through regular calls and meetings. The maintenance managers have undertaken a similar process to help share lessons learned from both outage and routine maintenance practices. These discussions and meetings have resulted in savings in the form of more competitive pricing structures when negotiating as a team as well as becoming more unified in the projects that each facility chooses to pursue.
Outage performance improvement was a top Cogentrix priority. The fall 2020 outage on Liberty 10 was difficult for the team as this was the first integrated large-scale outage for the sites. This first large outage event was a hot-gas-path inspection that led to numerous lessons learned. These lessons were shared and leveraged, not just for the subsequent outage at Liberty 20, but also at Patriot among both teams and contractors.
The team improved significantly from these events. Prior to the start of the spring 2021 outages, Cogentrix management reviewed all lessons learned with the operating teams, integrated the Siemens Energy input through its Total Maintenance Service (TMS) assessment process, and redesigned the outage execution structure as well as schedule adherence expectations. Cogentrix promoted two new general managers (previously the operations and maintenance managers) from within the organization, leveraging the strengths of each to gain buy-in on new processes. They worked together to implement the transition from the two sites working independently to being fully integrated.
The two sites, which previously had few common lessons learned, idea sharing, and support mechanisms, now have three shared positions, meet regularly, share metrics and goals, and leverage subject matter experts (SMEs) within their groups. Cogentrix incorporated industry best practices and fleetwide recommendations, and adopted practices to prevent similar issues in subsequent outages. This was done in rapid turnaround with a few months between the end of the first outage and the start of the remaining three. Other integrated staff changes included:
- ■ Following the purchase of the Hamilton assets, the role of the maintenance planner at each site was redefined with clearer expectations related to outage preparation and execution.
- ■ The roles of the Hamilton portfolio engineer and EHS manager were modified to better ensure that all safety, environmental, and compliance reporting and training were performed to the necessary standards and timeline.
- ■ The storeroom lead position became a shared role as well, with the goal of bringing consistency across the portfolio along with improving efficiency by having the two identical facilities purchase and share high-dollar critical spare parts.
- ■ A Siemens Energy resident engineer was added. The position shares time between both locations and is integral to day-to-day operations, issue resolution, and outage planning.
Other measures have led to further improvement in outage performance. For example, building on the Cogentrix relationship with Siemens Energy has been a key focus area to be able to optimize performance and outage management for the STG6-8000H units. Following the first hot-gas-path inspection, Cogentrix and Siemens Energy were able to take the lessons learned and reduce future outage durations. The majority of the improvements came from the better integration of site responsibilities and Siemens Energy work scopes.
Plant personnel also placed additional emphasis on communications of scheduled activity durations and activity handoffs for all on-site efforts, as well as impacts of various items to overall outage duration. This earlier tracking led to productive conversations and resource reallocation, as required.
Outage templates were developed utilizing the strengths of the planners from both locations and contractor expectations were more clearly defined. A “point-of-contact” role was defined, with expectations around how contract work is managed and how each job is turned back to operations. Job plan templates were developed to capture job procedures, contractor needs, parts needs, lockout/tagout needs, and turnover requirements. Additionally, outage jobs were assigned to operations and maintenance personnel for the development of these job plans.
As a result of these changes, outage durations have decreased and completion of scope has increased to include things like valve work, scaffold execution, and flow-accelerated corrosion high-energy pipe repairs. The operations and maintenance teams at both facilities are now working together on all aspects of plant maintenance and operational performance.
Cogentrix Long-Term Planning
In the Cogentrix operating model, the plant general manager is a key component for financial planning. Initially, the staff was not prepared to incorporate long-term capital improvements that integrated into the Siemens Energy recommended maintenance events. The new general managers learned the processes to build their budgets to align with Cogentrix corporate financial planning and ensure plant reliability. These philosophical changes don’t happen overnight and the staff continues to grow their skills using the financial planning tools and by leveraging the new communication channels that have been opened between the two facilities to maximize cost savings and ensure long-term maintenance plans are supported for the life of the plant.
Cogentrix has a longstanding and highly constructive relationship with Siemens Energy, including several plants that utilize Siemens Energy technology and are serviced under Siemens Energy LTSAs. Cogentrix was able to collaborate with Siemens Energy to restructure the Hamilton LTSAs and better define both routine maintenance and unit upgrade opportunities. The Patriot 10 rotor upgrade was the first under the new agreement and yielded a 30-MW improvement in unit output. This rotor exchange and unit upgrade was completed in the spring of 2021. The remaining Hamilton units are scheduled for the same rotor exchange and upgrade in 2025 and 2026.
In addition to the unit maintenance and improvement support, the restructured LTSAs extended the commitment of the Siemens Energy resident engineer. This position has proven to be a valuable communication tool between Cogentrix, Patriot, Liberty, and Siemens Energy. The resident engineer shares time between the two facilities and can respond to issues on-site with the full resources of Siemens Energy, including platform owners, engineers, and other specialist employees, who are the SMEs for these advanced machines.
Through the LTSAs, the Hamilton facilities continue to have full access to the Siemens Energy district service team, sales staff, and PDC group to ensure that all the engines in the portfolio are running reliably and meeting their design output. The plants are also involved with the Siemens Energy Alpharetta group for support of the T3000 distributed control systems (DCSs) and have recently entered a long-term Customer Service Agreement that includes a DCS upgrade to the latest version of the popular operating system in 2024. This agreement provides the team with 24-hour support and access to Siemens Energy’s controls system experts, similar to the level of support provided by the LTSAs. The relationship between the Hamilton portfolio and Siemens Energy has grown steadily to become an important partnership on key topics including training, O&M, and capital improvements.
Improved and Sustained Performance
In addition to taking over O&M and asset management responsibilities, the Cogentrix team also took over all aspects of commercial management for the Hamilton portfolio. This includes daily power and gas scheduling, hedging, capacity supply obligation management, and risk monitoring.
![]() |
3. The Liberty plant’s historical capacity factor, heat rate, Equivalent Forced Outage Rate – demand (EFORd%), and Equivalent Availability Factor (EAF) data from 2016 through 2022 is shown here. Courtesy: Cogentrix Energy |
Since Cogentrix assumed its O&M and energy management responsibilities, the plants have consistently achieved capacity factors near 90% (Figures 3 and 4) and have seen a significant improvement in financial performance. General Managers Sean Davis (Patriot) and Brian Zechman (Liberty) have been at the forefront of these efforts and are extremely proud of their teams and the work that has been completed in just a few short years.
![]() |
4. The Patriot plant’s historical capacity factor, heat rate, EFORd%, and EAF data from 2016 through 2022 is shown here. Capacity factor and EAF were negatively impacted by a planned outage in the second quarter 2021, during which a hot-gas-path inspection and Unit 10 uprate were conducted. Courtesy: Cogentrix Energy |
“Our team has grown in respect and trust of one another,” Zechman said. “Mutual respect and trust are two key ingredients in enabling our team to achieve goals aligned to a vision that moves us forward together and yields success.”
Building trust is also a key element in the Cogentrix model. The team extends beyond the plant fence lines, and the company believes employees need to see that in order to gain trust in the goals and expectations established. Cogentrix employees are encouraged to bring ideas to the table, and the company trusts them to have the capabilities and know-how to achieve measurable performance improvements. The general managers work to empower their employees to follow through on ideas with innovative solutions as well as simple fixes to long-term problems. This has fostered a long track record of internal promotions at the plant and corporate levels.
“Cogentrix has provided the Hamilton facilities with resources not previously available. These resources have included engineering, field support, and additional financing that has allowed both facilities to address equipment issues and pursue both safety and reliability improvements,” said Davis.
The Cogentrix team has completed many milestones since 2020. The integration of the plant staff, process reviews and implementation, and changes in overall operations philosophy have changed the day-to-day routines of all the site employees. These efforts have helped the Hamilton portfolio achieve industry-leading operating and reliability metrics over the past several years.
“I believe both Liberty and Patriot are on course to establishing themselves as the fleet leaders within Cogentrix and well-positioned to challenge others within the industry on safety, reliability, and performance,” said Davis.
—Mike Straubmuller is vice president of Operations with Cogentrix Energy Power Management LLC. Several members of the Hamilton team contributed to this article.
The post Optimizing Combined Cycle Power Plant Operations appeared first on POWER Magazine.