Commissioning and Acceptance Testing Are the Foundation for Total Electrical System Lifecycle Management
Credit to Author: Leif Hoegberg| Date: Wed, 01 Jun 2022 04:07:48 +0000
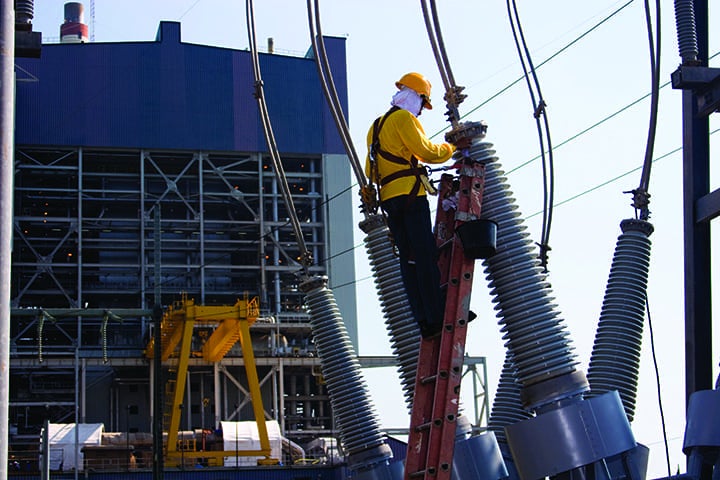
To manage the challenges of today’s complex electrical power systems and tightening budgets, facility managers need to understand the critical connection between electrical commissioning and acceptance testing, and planning for lifecycle management. To assist in this responsibility, this article will review the scope of services required for each stage of electrical system lifecycle management, and provide details on how proper commissioning and acceptance testing should inform the design of a maintenance program that fits the needs of a specific facility. It will demonstrate how the first stages of electrical system management can be used to establish an optimal maintenance program, set outage schedules, and plan for equipment life extension.
Electrical Commissioning and Acceptance Testing
Electrical commissioning (ECx) is the systematic process of verifying, documenting, and placing into service newly installed or retrofitted electrical power equipment and systems. Its purpose is to assure that tested electrical systems are safe, reliable, perform within manufacturer tolerances, are installed in accordance with design specifications, and conform with applicable standards.
Acceptance testing occurs concurrently with commissioning. It is the field-testing phase in which individual electrical components are assessed to verify their suitability for initial energization. Field tests and inspections are conducted to assure that the equipment and systems are as specified in the original design documents, meet manufacturer specifications, and are installed correctly.
ECx and acceptance testing should always be performed during new construction. In addition, similar procedures should be followed when there is an update to electrical equipment or system segments. This is critical to a successful system energization.
Working with experienced field technicians and electrical engineers will ensure that the appropriate scope of ECx and acceptance testing services is performed relative to national standard recommendations/requirements and specifications. These experts will also be able to provide a comprehensive analysis of the facility, identify efficiency opportunities, and conduct both a reliability analysis through the identification of single points of failure and an end-of-life analysis of equipment.
The ECx and acceptance testing phases are a collaborative process in which both the facility owner and the commissioning/acceptance testing organization/team have unique responsibilities. The American National Standards Institute/InterNational Electrical Testing Association (ANSI/NETA) standards outline these responsibilities in detail.
Owners must provide the commissioning and acceptance testing team basis of design (BOD) documents, electrical single-line diagrams, engineering studies, hazard notifications, and safety training documentation. The commissioning and/or acceptance testing organization/team provides the technical expertise to conduct all necessary inspections, evaluations, component tests, analyses, and reports. This is in order to execute the electrical commissioning and acceptance testing process according to industry standards and manufacturer instruction manuals. The process ensures a comprehensive scope of work and produces a written record of all commissioning and acceptance testing activities, and a final report.
The ECx and acceptance testing scope includes the following:
- Development of a project commissioning schedule, including design, construction, acceptance testing, occupancy stages, and key commissioning milestones.
- Description of commissioning activities that will occur during pre-energization, energization, and post-energization.
- Creation of commissioning and acceptance testing checklists, test plans, and test forms specific to the project.
- Visual and mechanical inspections.
- Electrical acceptance tests.
- Documentation of the commissioning process.
- Commissioning and acceptance testing reporting.
- Documentation of test parameters.
- Reporting on testing results.
- Documentation of approval by the facility owner and operator to allow the equipment to be energized.
Building a Better Maintenance Program
The ECx and acceptance testing procedures, if executed properly, will provide the foundation for creating a customized maintenance program, which will lead to optimizing power performance, minimizing downtime, and maximizing life expectancy. The ECx process sets up the proper engineering studies and documentation needed during regular maintenance and whenever system changes are required. The acceptance testing datasheets establish equipment lists, and document instrument settings, which can be used to set up the recording process for ongoing maintenance and test results (Figure 1). Additionally, access to the acceptance testing data during maintenance provides a reference to baseline metrics and settings. This shortens the test interpretation, analysis, and system health evaluation process.
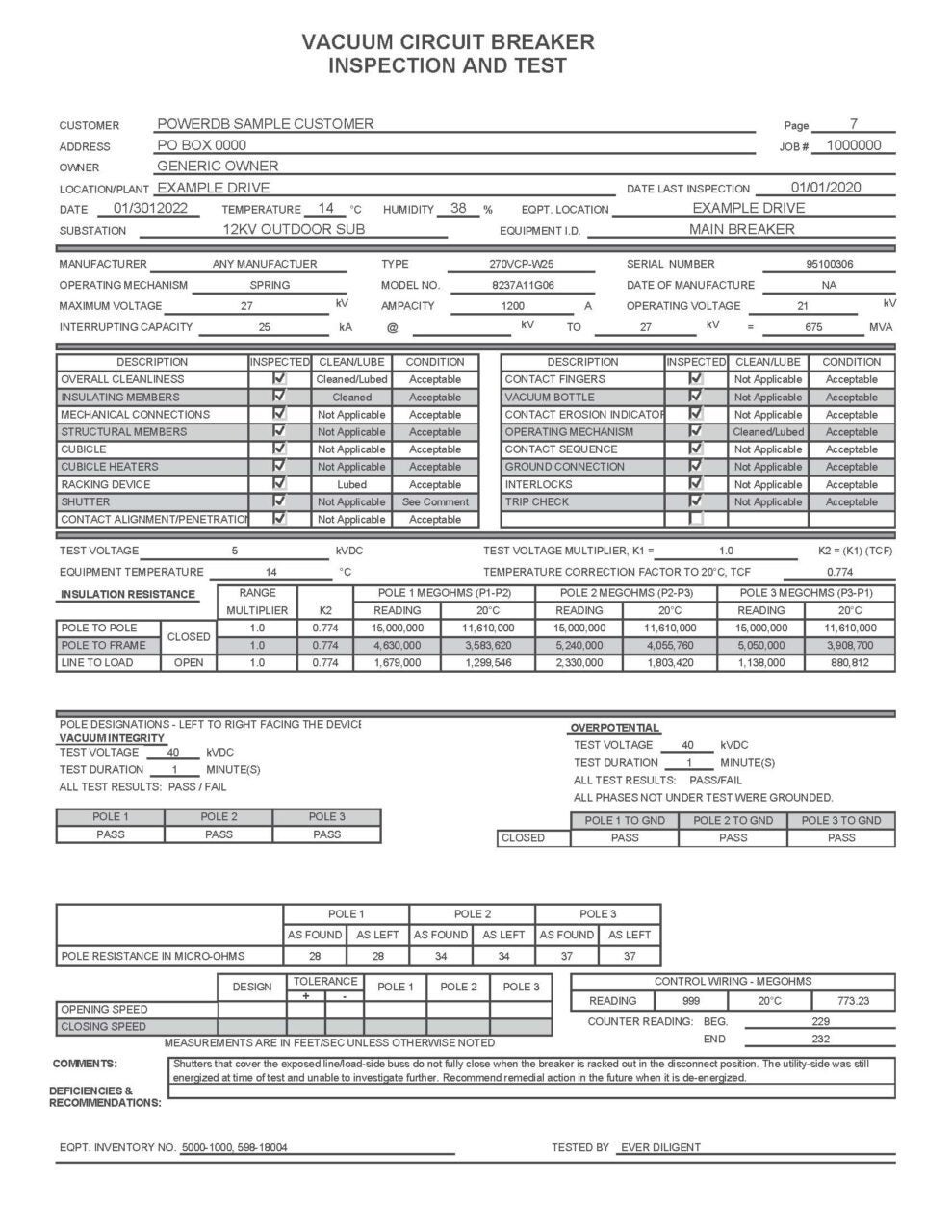
Another advantage of being able to cross-reference ECx, acceptance testing, and maintenance data is that it facilitates long-term tracking of equipment health against benchmarks, equipment averages, and detailed monitoring of equipment performance over time. Acceptance testing documentation also includes the necessary component information needed when equipment is repaired, retrofitted, or replaced.
Throughout an electrical system’s lifecycle, it can be useful to utilize electronic database programs, such as PowerDB, to record acceptance and maintenance test results, and house documentation allowing for long-term storage and easy access. These types of data hosting programs can be a time and cost-saving solution as equipment ages and maintenance personnel change. Most data management programs allow maintenance managers to compare assets across the facility to gain an understanding of the relative equipment health and to determine how best to prioritize equipment maintenance, repairs, or replacements.
One of the challenges of designing an optimal maintenance program is determining the maintenance intervals for system segments and components. With ECx and acceptance testing data readily available, it becomes a simple process to utilize Frequency of Maintenance Tables to build out justified and standard compliant maintenance schedules.
The Frequency of Maintenance Tables can be found in the ANSI/NETA Maintenance Testing Standard, Appendix B (Figures 2 and 3). Guidance is also provided in the National Fire Protection Association (NFPA) 70B standard, Recommended Practice for Electrical Equipment Maintenance. The NETA tables require an evaluation of the criticality of the electrical system or system segment application—low, medium, or high—and an understanding of the condition of the equipment—poor, average, or good. Based on these equipment parameters, the tables provide recommended maintenance intervals for every type of electrical power asset.
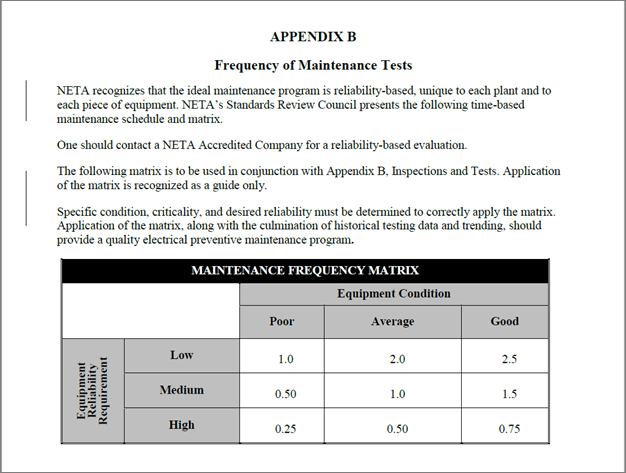
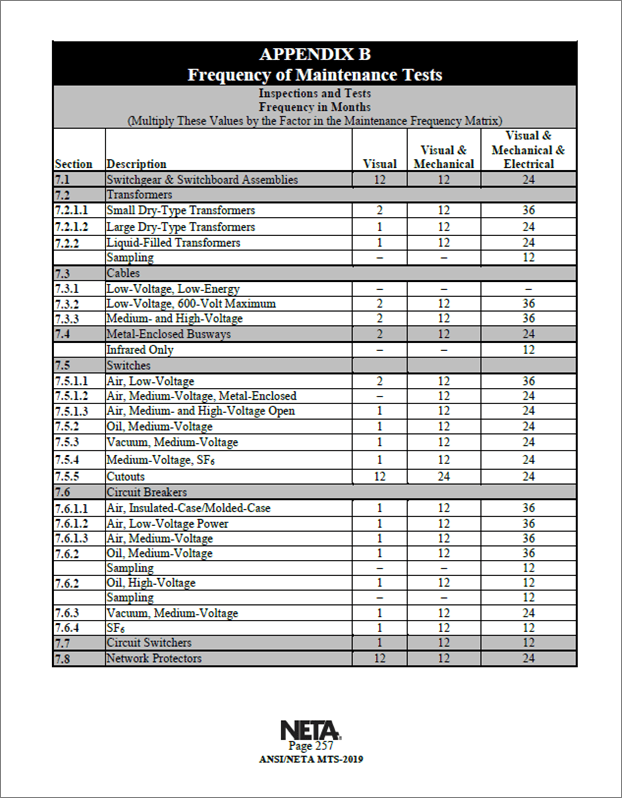
Maintenance Assessment and Testing
Maintenance assessment and testing is the longest phase of an electrical system’s lifecycle. As important as ECx and acceptance testing is, routine maintenance is as critical to the operation and optimal performance of existing electrical systems. Maintenance includes component and interconnection tests to ensure that the systems and apparatuses perform satisfactorily. Regular maintenance provides an understanding of the condition of the systems and their equipment, and it also identifies potential problem areas before they become safety concerns or major issues requiring expensive and time-consuming solutions.
If proper ECx and acceptance testing are performed, then maintenance work following new construction, retrofit, expansion, or replacement projects can ensure that equipment and systems are operational within applicable standards and manufacturers’ published tolerances. Visual inspections and comparison to accurate single-line diagrams and design specifications allow for confirmation that equipment and systems remain in alignment with the facility’s power needs and operational requirements.
Maintenance Assessment and Testing Scope includes:
- Power system studies.
- Inspection and test procedures on all equipment.
- System function tests.
- Thermographic surveys.
- Online partial-discharge survey for switchgear, cables, and transformers.
As with the ECx and acceptance testing phases, maintenance assessment and testing should also be a collaborative process between the owner and the testing team; each has unique responsibilities.
Owners are responsible for providing equipment in a ready-to-test condition. They must provide engineering studies, arc flash studies and up-to-date labeling, protective device settings, itemized description of equipment, site-specific hazard notifications, and employee safety training.
The testing organization/team is responsible for providing testing expertise, testing tools, and all maintenance requirements noted above under the Maintenance Assessment and Testing Scope. Additionally, the testing organization provides a record of all tests, final reports, notifications, and recommendations related to deficiencies found in the maintenance testing process.
Life Extension
The assets that make up the electrical distribution system will eventually become worn or obsolete, especially when considering today’s rapid rate of technological advancement. Aging electrical systems present a variety of concerns for today’s asset managers. These systems have higher maintenance requirements that not only cost more to maintain but also pose a greater risk of failure and higher safety risks for personnel.
Fortunately, there are many cost-effective solutions that include upgrading and retrofitting existing electrical assets to extend the life, and improve system performance and reliability with the latest technology. Planning ahead for life extension and component upgrades allows for proactive management of a system’s lifecycle in order to maintain optimal performance and leverage equipment advancements. Executing a planned life extension program delivers many benefits, leading to long-term cost savings and improved operational reliability. These benefits include:
- Extending the useful life of system assets.
- Returning assets to optimum operating levels.
- Ensuring compliance with all applicable standards.
- Increasing workplace safety.
- Planning for technological advancements.
- Improving access to system information and monitoring ability.
A routine preventive maintenance plan paired with a proactive life extension program will maximize an electrical system’s lifecycle. Periodic maintenance protects components from the adverse effects of heat, dust, moisture, and other contaminants. Problems are identified before issues or failures occur. Life extension services keep equipment operating at peak performance, ensure protection schemes perform when needed, and help progressively manage facility and system updates.
The Life-Extension Service Scope can include:
- Refurbishment services, which include visual and mechanical inspections, cleaning and lubricating of all mechanisms, electrical preventive maintenance testing, and electrical function testing.
- Reconditioning services, which include resurfacing of insulation or equipment surfaces, inspection and/or disassembly of all parts for physical integrity, and replacement of worn parts.
- Rebuilding services, which apply to circuit breakers, switches, starters, contactors, and motor control centers; and include re-plating, polishing, replacing of hardware, and painting.
- Retrofitting services, which include upgrading of equipment that can be integrated into the system’s existing footprint and power scheme. This can include circuit breakers, trip units, relays, and uninterruptible power supply (UPS) systems.
No matter where a system is in its lifecycle, the cost to keep equipment in operation can continue to rise despite the best efforts to maintain the equipment. Life extension services can delay the system’s wear-out status. It can help maintain optimal power performance through systematic reconditioning, upgrades, and replacement of components, which negate the probability that multiple components will fail or become obsolete at the same time. Scheduling system upgrades proactively also allows for capital investment planning for new technology that will enhance performance along with asset value.
The Quality of Electrical System Lifecycle Management Services
The ANSI/NETA Standards for Electrical Commissioning, Acceptance Testing, and Maintenance Testing Specifications for Electrical Power Equipment and Systems were developed for use by those responsible for the operation of electrical systems and equipment. These standards guide owners, engineers, contractors, and service providers when specifying and performing the necessary analyses and tests to ensure that electrical systems and apparatus perform satisfactorily, minimizing downtime, and maximizing life expectancy.
The NETA standards also provide specific recommendations regarding the capabilities and qualifications of services providers and field technicians. These specifications are provided to ensure that the proper scopes of work are performed in accordance with national standards. They cite the following:
The NETA standards recommend that owners utilizing testing companies should require that each onsite crew leader shall hold a current certification, Level 3 or higher, in electrical testing. This certification is in accordance with the ANSI/NETA ETT, Standard for Certification of Electrical Testing Technicians.
Owners utilizing manufacturers’ service personnel should be certified by the manufacturers to perform these electrical tests and inspections. The manufacturers should provide sufficient documentation to satisfy the owner that their service personnel are trained and qualified to perform these electrical tests and inspections.
Owners having in-house testing personnel should utilize an independent, outside certification organization or have a system of qualification which provides an equivalent level of assurance that their personnel are qualified to perform electrical testing.
The above specifications aid in ensuring workers are properly trained and have the experience to support lifecycle management objectives and to ensure the safe, reliable operation of electrical power systems and equipment.
Electrical Standards and GuidelinesECx, Acceptance Testing, and Maintenance Assessment and Testing related organizations providing standards and guidelines for best practices include:
|
—Leif Hoegberg is director of Engineering and Technical Support for Electrical Reliability Services Inc. He has more than 30 years of electrical engineering, operations, and field service experience. Hoegberg is a Level IV NETA-certified technician, serves on the NETA International Electrical Testing Association’s Standard Review Council, and is a member of IEEE, NFPA, and the International Association of Electrical Inspectors (IAEI).
The post Commissioning and Acceptance Testing Are the Foundation for Total Electrical System Lifecycle Management appeared first on POWER Magazine.