Small Modular Reactors Provide Opportunity to Rethink Automation for Nuclear Generation
Credit to Author: POWER| Date: Mon, 02 May 2022 04:15:00 +0000
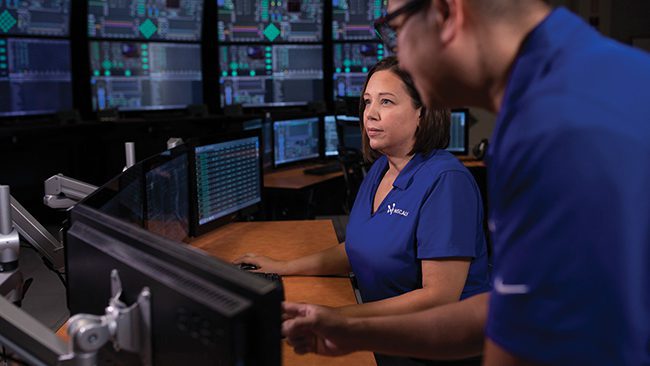
An emerging generation of small modular reactors is encouraging suppliers and regulators alike to consider new digital instrumentation and control approaches.
While instrumentation and control (I&C) technology represents a relatively small percentage of the overall capital investment for any nuclear power station, it often plays an outsized role for safe, reliable, and efficient operation. Recognizing the potential benefits, the U.S. Nuclear Regulatory Commission (NRC) and other regulatory agencies have become more open to digital I&C technology in nuclear facilities.
The new wave of small modular reactors (SMRs) currently in development are particularly ripe for new digital technology solutions. SMRs offer cost, siting, and safety benefits relative to full-scale nuclear generating plants, but will lack comparable economies of scale. This is particularly true when it comes to staffing for operations and maintenance (O&M) functions. And while SMRs are designed to reduce the need for human intervention should something go wrong, ample opportunities remain for new digitally enabled automation technologies to improve SMR performance, reduce O&M costs, and further improve overall safety.
Guy Anderson, Chief Nuclear Officer of Moltex Energy, which is developing Canada’s 300-MWe Stable Salt Reactor-Wasteburner (SSR-W) SMR, stressed that wherever possible, the company’s approach is to utilize the inherent design characteristics to provide most control and safety functionality. He believes that while instrumentation will still be needed, it will be used mainly to support monitoring and display functionality for the operators.
According to GE Hitachi’s Jon Allen, the company’s BWRX-300 SMR “places limited demands on the operator compared to the existing LWR [light water reactor] fleet because it is a natural circulation BWR [boiling water reactor] with passive safety systems that provide at least seven days of coping time without operation actions.”
Diane Hughes, NuScale Power’s vice president of Marketing and Communications, commented that “the NuScale Power Module design is very safe and simple to operate with no operator actions or complicated automated sequences needed for safety.”
Holtec’s SMR-160 is also designed to minimize the load on operators should an accident scenario arise. The reactor is passively cooled for design basis shut down. The reactor coolant system continues to circulate by thermo-siphon action during accident scenarios.
Bayen Rafeh from the I&C group at nuclear services and technology supplier, Framatome, agreed that less human intervention will be required in the normal operation of SMRs and that the simplification and integration of components and architecture also means that fewer functions will have to be implemented, reducing the need for automation equipment.
SMR Automation Trends
Due to the inherently simplified nature of SMRs, suppliers envision that new automation and information technologies will be leveraged not so much to reduce the basic process control burden on operators as to provide supervisory control functionality to enhance situational awareness and support multi-module planning and dispatch functions.
Read about how Duke Energy and Purdue University are looking at how small modular reactor technology could power the school’s Indiana campus.
According to Patrick Essner, team leader for Holtec’s electrical and I&C group, “Multiple plant loads create new challenges for operators. There definitely are opportunities to use new technology. Holtec will use the latest available technology that has been approved for nuclear service.”
The I&C and human-machine interface (HMI) for GE Hitachi’s BWRX-300 will be evolutions of the company’s recent designs. According to Allen, “Current protection, control, and monitoring with their associated HMI design approaches will be used following proven guidelines and practices. HMI optimization ensures that the operations staff can be lean.”
Centralized Control Rooms for Multiple Reactor Modules
To facilitate reduced operations staff and enable fewer operators to simultaneously monitor and control multiple small modular reactors within a common SMR facility, most will have central control rooms (Figure 1).
![]() |
1. NuScale’s control room simulator consists of 12 reactor control terminals and operator workstations. The simulator was used in the design certification process to analyze the human-machine interface design and controls system strategy, and to develop operating procedures. Courtesy: NuScale Power |
Hughes at NuScale Power, which is developing the 77-MWe NuScale Power Module, commented, “Most nuclear plants in the U.S. consist of a single- or dual-reactor arrangement and regulations currently limit the number of reactors that can be controlled from a single control room to two and have limited digital control. SMR control rooms will likely be fully digital and change the paradigm of operation that exists in current analog nuclear power plant control rooms. … NuScale developed the information needed to obtain NRC approval that allows up to 12 NuScale Power Modules to be operated from a single control room.”
According to Essner at Holtec, “Our overall goal is to make the system simple and safe to operate.” To this end, there will be a single operator interface across the plant. Overall control philosophy is to centralize the control room to simplify operation and make the operators more efficient. The safety and non-safety systems are separate but can communicate with each other to simplify operation. “The control system basically is a centralized controller and control room with remote I/O [input-output] cabinets.” He added that the relatively small size of the plant means the cabling requirements are much simpler than in a full-scale nuclear plant.
Framatome envisions that multi-module SMR plants can share a main control room but will require extensive human factors engineering and simulation in the early stages of design.
Factory-Installed Instrumentation
Since the SMR concept calls for reactor and other modules to be manufactured in the factory and then shipped to site for final assembly, the question arises whether this also means that much of the instrumentation and associated cabling would also be installed and verified at the factory.
According to Hughes, the instrumentation for the NuScale Power Module associated with protection and control processes will be embedded as much as practicable during fabrication and assembly at the factory. However, the I&C components for the balance of the plant will be installed during plant construction activities.
According to Holtec’s Essner, “The goal of modularity is to simplify plant construction. This includes taking advantage of factory-installed instrumentation where it makes sense to do so.”
GE Hitachi and Moltex also plan to install at least some instrumentation at the factory.
Commercially Available Safety and Non-Safety Systems
As required by the nuclear regulatory agencies, SMR facilities will continue to utilize separate, disparate, and largely independent systems as appropriate for safety and non-safety plant applications. While many of these systems will be based on well-established commercially available platforms, others will utilize custom-developed solutions.
NuScale’s safety-related protection system platform is based on Field Programmable Gate Array (FPGA) technology. The system utilizes a patented remove-power-to-actuate design. The non-safety control systems, in contrast, will be supplied by a vendor that NuScale will reveal in the coming months. This will leverage the extensive design and testing NuScale has performed when developing the company’s power plant control room simulator.
Holtec has partnered with Mitsubishi Electric in Japan to use that company’s MELTAC Nplus S digital safety controller for safety-related controls and MELTAC-RX system for non-safety controls. These systems have been qualified in Japan and accepted by the U.S. NRC for digital safety systems.
GE Hitachi is taking an International Atomic Energy Agency (IAEA)- and International Electrotechnical Commission (IEC)-centric approach that provides “a clear, explicit, and justifiable safety strategy approach with deterministic and risk-informed lines of defense.” The company believes this framework supports implementation of modern digital I&C solutions because both the architecture and risks are more understandable to the nuclear regulators and other stakeholders. The controls in the Safety Class 2 and 3 and non-safety I&C systems will be commercially available hardware and software. Safety Class 1 will be a mix of commercially available and proprietary systems.
Moltex is designing on the basis that standard digital industrial process control technology will be used for control and monitoring systems. However, it is likely that any protection equipment will be hard wired. Moltex is in discussions with several companies to determine their suitability as preferred instrumentation and component suppliers.
Framatome’s modular, commercially available digital safety platform, Teleperm XS Compact, was designed for small and decentralized Class 1 systems, making it appropriate for SMR applications. According to the company, the simplicity of its design simplifies qualification. The company also offers its Hardline non-programmed safety platform plus a neutron instrumentation system.
Simulators Gaining Traction
While simulation technology has been utilized with the nuclear power industry in some manner for decades now, the technology really appears to be coming into its own for SMRs. This includes the use of high-fidelity simulators to support regulatory agency acceptance as well as for upfront engineering and design, optimization, and ongoing O&M.
NuScale, for example, has built a control room simulator that the company used to test and demonstrate that the new digital interface is safe and effective for plant operations. Holtec will use simulators to pre-validate its systems at the factory. Framatome’s subsidiary, CORYS, has been supplying training and engineering simulators to the power and other industries for more than 30 years.
Remote Monitoring and Diagnostics
Since many SMR facilities are likely to be built in remote locations and have limited on-site resources, remote monitoring and diagnostics capabilities would appear to be an excellent fit once the associated cybersecurity and regulatory hurdles are overcome.
According to Hughes at NuScale, “Analytics, machine learning, and artificial intelligence can all be leveraged to optimize the predictive maintenance models to maximize reliability and minimize cost and downtime.” NuScale’s service delivery program will also be able to provide a central repository for all customer operating and maintenance data, enabling the company to fine-tune the predictive maintenance program across its future fleet of plants.
“Advanced condition monitoring systems to acquire, organize, and archive plant process data with their downstream analytics applications are essential to enable condition and predictive maintenance solutions,” said GE Hitachi’s Allen. GE Hitachi is also working to incorporate the needed instrumentation into its design and address cybersecurity concerns to be able to take advantage of GE’s established strengths in remote monitoring and predictive maintenance across a variety of industries.
More Innovations on the Horizon?
SMRs can play an important role in the transition to renewable, carbon-free power generation. They represent a new and potentially more sustainable paradigm for the nuclear generation industry. However, it appears that there’s still plenty of room for technology innovation at multiple levels, from basic I&C through HMI, supervisory control, and plant optimization. Assuming that the relevant regulatory agencies succeed in their current efforts to simplify and streamline the technology review and approval processes, it’s likely that we’ll soon see additional innovations emerge in the I&C/automation space.
—Paul Miller has been following technology and industry trends in the power, oil and gas, chemical, and other process industries for more than 35 years, most recently as content director at ARC Advisory Group, a leading global market research and technology consulting firm.
The post Small Modular Reactors Provide Opportunity to Rethink Automation for Nuclear Generation appeared first on POWER Magazine.