Making Power Plants Purr or Putting Them to Sleep: Hard Equipment and Soft Tools
Credit to Author: Kennedy Maize| Date: Fri, 01 Apr 2022 04:07:00 +0000
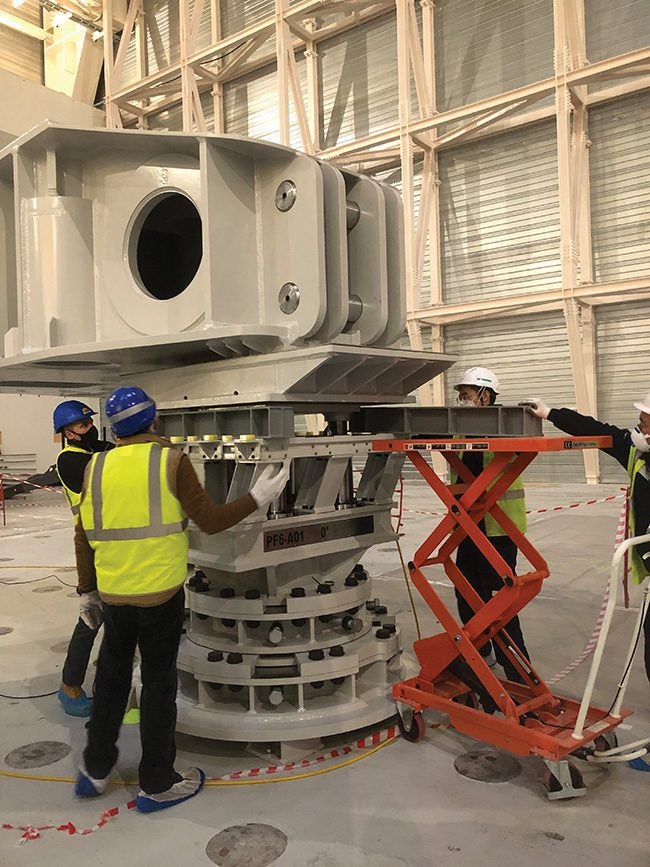
Maintenance equipment and tools have always been important for plant operators. In the early days, the tools were likely made entirely of iron and steel, copper and brass, lead, leather, rubber, or glass. Some of those tools still apply, but now digital solutions also play a role in managing efficient operations and maintenance departments.
From the beginning of electric power production in the late 19th century, plant operators and maintenance staff have aimed to keep units running in top shape. That goal remains. In a sports analogy, the idea is to keep the plant in the game, not on the injured reserve list. Or, when their useful life is over, to retire them.
![]() |
1. Enerpac hydraulic cylinders are set to have a key role in the final construction of the ITER fusion tokamak in 2024. On completion of assembly of the tokamak’s vacuum vessel sectors, nine cylinders—now pre-installed at the bottom of the machine—will lift an 11-meter-diameter, 320-ton, circular poloidal magnet (PF6) into position at the base of the tokamak. Here workers are shown testing the Enerpac EVO systems and stack beam lifting process for raising the PF6. Courtesy: Enerpac |
There is plenty of life left in the hard tools of all sizes, still required for plant maintenance, construction, and destruction. Just take a look at the Enerpac catalog of tools and equipment useful in the power industry. Among the items, you’ll find a self-propelled modular trailer capable of moving a 14-foot-diameter, 3-foot-thick steel plate through a narrow passageway of a reactor building equipment hatch, providing a radiation shield at the bottom of a nuclear reactor head assembly. You’ll also find a hydraulic lift system for leveling and supporting offshore wind turbines in the turbulent North Sea off Germany. And if you can’t find what you’re looking for, you might be able to collaborate with the company to develop a solution (Figure 1).
Enerpac Tool Group has a market capitalization of $1.08 billion and more than 2,100 employees. The company recorded $131 million in sales for the first quarter of fiscal 2022. Founded in 1910, the company says its “businesses are global leaders in high pressure hydraulic tools, controlled force products and solutions for precise positioning of heavy loads that help customers safely and reliably tackle some of the most challenging jobs around the world.”
Jason Jones, Enerpac Tool Group director of strategic sales, told POWER that sales to the power industry, both through dealers, direct sales, and manufacturing tools, amounts to roughly 15% to 20% of the company’s sales. He noted, “Wind turbine sites require large equipment,” and as the wind power industry evolves, turbines become bigger to produce more power per turbine. Gas turbine business has seen a “significant increase in production and safety” issues. Nuclear has seen a “consolidation within single sites.”
Power plant physical tools include cylinders, pumps, hydraulics, bolting tools, machining, mining, and skidding. In general, it’s all about heavy lifting. Those tools often require the use of brute force, employed by skilled workers who understand how to use the equipment effectively. Physical force, applied with brains and experience, gets work done. Even lesser tasks require trained personnel using sophisticated tools, whether hand tools or larger equipment.
The tasks these physical equipment and tools serve are often difficult to manage. Scheduling complexities, staffing status, and ancillary resources all complicate the tasks. One commentator noted that “organizing all of that work is tough—if not impossible—to do manually.”
Digital Tools
Many of today’s power plant maintenance tools are not physical. They are built of 0s and 1s, not iron and steel. Digital, built to organize and manage all that hard physical work. Computers and computer software have revolutionized maintenance and its management, helping to deploy the physical tools.
Initially primitive, digital tools for power plants have evolved over some 20 years into sophisticated, versatile, and often cloud-based products, offered by many vendors. As the SelectHub website explains, “Power plant software fits into the category of computerized maintenance management systems (CMMS). More specifically, since it’s a specialized type of asset management software and computer-aided facility management software, it helps you control your whole power plant.”
“In a nutshell,” says SelectHub, “the software helps you control almost every aspect of your power plant. This includes organizing maintenance, scheduling workers and collecting various types of data. Asset management features are among the most prominent, as performing preventive maintenance is one of the most important tasks of power plant management.”
The software doesn’t do heavy lifting, but it does tell you when, where, how, and how often to perform routine tasks, and when, if necessary, to apply the muscle. Eagle Technology Inc., vendor of Proteus MMX, a highly rated CMMS product, outlines the role of CMMS software:
- ■ Decrease equipment downtime.
- ■ Help ensure safe and effective power generation operations.
- ■ Meet regulatory and compliance standards.
- ■ Extends the life of power generation assets.
- ■ Minimize investments in inventory.
CMMS software is an example of the touted “Internet of Things,” or IoT. The systems use the online network to transfer data from the equipment to the software to management to use in making maintenance decisions.
While well adapted to power plant operations, many CMMS packages also work in other major industrial facilities, including chemical plant operations. While power plants and chemical plants are very different, they have many common features, including complex maintenance systems working under high-stress conditions, with high temperatures, pressures, and weights. They have daunting maintenance management and scheduling tasks.
An article published in POWER in 2017, accompanying the first Connected Plant Conference—the 6th annual conference is scheduled to take place in Atlanta, Georgia, May 23–26, 2022—noted how Duke Energy has used software “to detect equipment failures earlier than was previously possible,” noting that “the earlier problems are detected, the more time there is to plan, prioritize, schedule, and execute repairs.” A Duke executive said, “We have many sensors applied on our assets. They’re hardwired to numerous data acquisition systems around the station. Those data acquisition computers then send information to the plant server wirelessly. If we didn’t have that architecture, it would be far too expensive to install this, because really 75% of the cost of the project is related to installation of the wiring for the sensors—and that’s just for a very short distance to these computers.”
A dozen or so CMMS packages are suited for power plant operations. Several online sites, including SelectHub, Capterra, and Software Advice offer comparative ratings of CMMS packages. It’s vital to investigate the products in detail before making a financial commitment, although the costs are small compared to the big-iron equipment.
Several raters rank the CMMS systems, but Capterra’s scoring seems to be the most complete. Capterra judges the system’s capabilities on “billing and invoicing, calibration management, inventory management, key and lock management, mobile access, and preventative maintenance.”
![]() |
2. Among computerized maintenance management systems available on the market today is Eagle Technology Inc.’s Proteus MMX. Last year, the company announced the full integration of Proteus MMX with Esri’s ArcGIS (geographic information system) software for location intelligence. The combination provides numerous benefits, such as finding assets, capturing data, and tracking patterns in data. Courtesy: Eagle Technology |
The top-rated Capterra and Software Advice product is eMaint CMMS from Fluke Reliability. The eMaint system ranked second at SelectHub, where Proteus (Figure 2) is on top. Fluke is a vendor of a wide array of electronic tools, including imagers and meters. It checks all six of the Capterra categories. It is cloud deployed, and available in Apple and Windows applications but not Linux. It is also in the low-cost category.
SelectHub says eMaint software works for “tracking, managing and controlling assets, work orders and requests. It includes workflows, inventory and spare parts, maintenance management, monitoring for equipment condition and regulatory compliance support. It’s suitable for companies of all sizes and serves many industries worldwide, including manufacturing, oil and gas, healthcare, and education.” Other rated systems include Fiix, Limble CMMS, FTMaintenance Select, Hippo CMMS, simPRO, and more.
The Future for Power Plant Equipment and Tools
Power plants in the future, whether conventional or advanced, including fossil, nuclear, or renewables, will need construction and decommissioning assistance, and plant maintenance. Construction will require the big iron: heavy lifting, major equipment moving, and installation of repair and replacement parts.
New wind turbine blades require ways to put them into place. Wind plants, both on land and increasingly offshore, will need assistance to get them situated. Solar systems will need construction help and maintenance.
All that hard work will need software to assist and guide operations. SelectHub market analyst Pratiksha Thayil wrote, “As we look ahead to the future of power plants and the future of power plant software, it looks a lot brighter than it did not all that long ago. There are still challenges and uncertainties ahead, especially as renewable energy continues its growth. But when armed with power plant software that provides the right features, plants will be able to improve and adapt to our ever-changing world.”
There likely will be a melding of hard equipment and soft tools. A recent International Atomic Energy Agency (IAEA) survey concluded, “Operators and authorities in more and more countries are moving to immediately dismantle their retired nuclear facilities, and emerging digital technologies coupled with greater usage of robots and drones are offering significant potential for more effective project implementation and risk reduction.”
The IAEA said, “Technologies such as 3D modelling or building information modelling (BIM), virtual reality and remotely controlled technologies, including drones and robots, are also being applied increasingly to the decommissioning of facilities that have reached the end of normal life. These technologies enable more efficient collection, understanding, display and management of data, allowing different scenarios to be visualized during planning and preparation of dismantling and decontamination activities.”
Enerpac Tool Group’s Jones said his company sees wind as a big growth opportunity, and also foresees coupling equipment with digital monitoring. For wind, he said, operators will want to monitor the physical load on the turbines remotely, so they won’t have to send crews to check out the machines manually.
He also sees a definite movement into rapid deployment of power plant infrastructure, with “modular units built offsite,” and then assembled onsite, saving construction time and money. Assembly will mean heavy lifting. He said Enerpac is working with nuclear small modular reactor developers Holtec International and NuScale Power to provide at least a couple of solutions.
Jones added that 3D printing is beginning to make a significant impact on his company. It “has transformed how we manufacture some of our tools,” so they can be made “very quickly.” The company started with 3D printing of plastic handles, but “are now getting into metallic” components.
—Kennedy Maize is a veteran energy journalist and frequent contributor to POWER magazine.
The post Making Power Plants Purr or Putting Them to Sleep: Hard Equipment and Soft Tools appeared first on POWER Magazine.