Low-Cost Long-Duration Energy Storage at a Natural Gas Pipeline
Credit to Author: POWER| Date: Tue, 01 Mar 2022 05:10:00 +0000
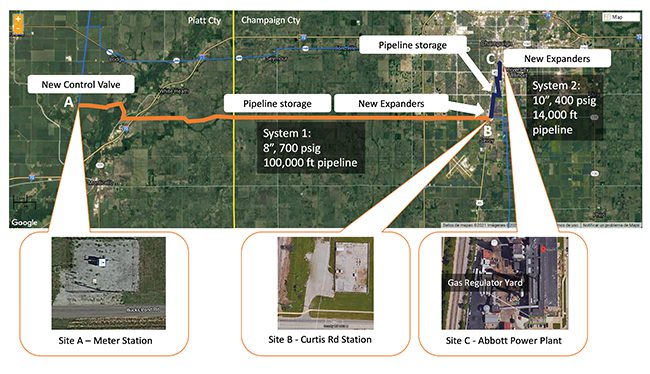
An energy storage project based on Compressed Natural Gas Energy Storage (CNGES) technology is being studied at the Abbott Power Plant in Illinois. This article presents an overview of CNGES technology, assessment of the potential of implementing it at an existing pipeline, and preliminary results obtained from the Department of Energy–funded Abbott Power Plant study.
One of the U.S. Department of Energy’s (DOE’s) current priorities is the development of low-cost, reliable, long-duration energy storage. U.S. Secretary of Energy Jennifer Granholm announced the “new goal to reduce the cost of grid-scale, long-duration energy storage by 90% within the decade,” as the U.S. is preparing “to bring hundreds of gigawatts of clean energy onto the grid over the next few years.”
In line with this goal, the Illinois Sustainable Technology Center (ISTC) of the Prairie Research Institute (PRI) of the University of Illinois Urbana-Champaign (UIUC) is completing a conceptual (Phase I) DOE-funded study. The project will implement energy storage to the Abbott Power Plant (Figure 1). The asset is an 84-MW and 800,000 pounds per hour of steam (lb/hr) combined heat and power (CHP) plant owned and operated by the university. The energy storage concept designed for the site is based on compressed natural gas energy storage (CNGES) technology, which was developed by the ECOTEK group of companies. The ISTC team also includes Enerfex Inc. (systems integration) and Visage Energy LLC (market commercialization assessment and business case development).
![]() |
1. Abbott Power Plant is an 84-MW and 800,000 pounds per hour of steam combined heat and power plant owned and operated by the University of Illinois Urbana-Champaign (UIUC). Courtesy: UIUC |
Storing and Recovering Energy at Natural Gas Pipelines
CNGES is a derivation of the more general compressed gas energy storage (CGES) technology, which operates by increasing the pressure of a compressible gas inside a control volume during off-peak periods and discharging this inventory of gas to a lower pressure through a turboexpander coupled to an electrical generator during peak demand periods. Ideally, the process requires little or no combustion, depending on site characteristics.
CGES can be applied with any gas, but the economics are most favorable with gases that have widely developed infrastructure. The implementation of gaseous fuels as working fluids provides an additional advantage because their chemical energy (heating value) can be ultimately transformed to electricity by integrating the energy storage technology with a power generation plant. Widely developed networks and use in the energy system both favor the use of natural gas and serve as the rationale for deployment of CNGES.
The U.S. natural gas network is comprised of roughly three million miles of mainline and other pipelines, and delivered about 27.7 trillion cubic feet of natural gas to about 77.3 million customers in 2020. Approximately 1,700 midstream natural gas pipeline compressor stations are used to transport this gas, and more than 10,000 pressure reduction stations deliver the gas at safe pressure levels. More than 400 underground storage sites provide resiliency. Virtual pipelines offer alternative paths to circumvent pipeline restrictions.
This gives CNGES deployment a key advantage when compared to other energy storage technologies because it can capitalize on widely available utility assets. Existing natural gas infrastructure can be utilized to perform two steps in the CNGES process: “charging” by raising the pressure of the gas through existing compressors, and “storing” by utilizing an underground field, aboveground vessel, or a flowing pipeline. The third step, “discharging” can be deployed by harnessing available pressure differentials at existing pressure reduction stations with the installation of new expander generators.
This advantage of CNGES becomes clear when comparing it against another mature energy technology: compressed air energy storage (CAES). Although CNGES and CAES share the same process steps (compression, storage, and expansion), a CAES project typically involves the development of completely new infrastructure for all three process steps, may be limited by the availability of suitable storage sites, and depends primarily on the price spread between peak and off-peak electricity for revenue. In contrast, CNGES avoids the cost of two of the three process steps by integrating with existing infrastructure and can benefit from price dynamics of both the electricity and natural gas markets.
Deploying CNGES at a Pipeline
The components of a CNGES system can be subdivided into charging, storage, discharging, and auxiliaries/balance of plant. When adapting a natural gas pipeline for CNGES, these three parts are typically not co-located: charging and discharging can be located several miles apart. Auxiliaries need to be provided on both ends of the pipeline and coordination between each section is handled via a control system.
Charging. Charging is the process of transforming electrical energy into potential energy (higher pressure) plus kinetic energy (movement). For CNGES, this process occurs at natural gas compression stations.
CNGES requires electrical motor-driven compressors. Existing natural gas compressors driven by combustion turbines or engines can also be converted to electrical energy by replacing the driver for an electrical motor or to hybrid by installing a clutch that enables the operator to select between electrical and combustion drive.
The controls are adapted so that the compressor load increases during off-peak demand or during clean energy peaks and decreases during peak demand. This type of operation minimizes costs by capitalizing on the electricity price variations or clean peak standards.
Storage. Storage is the process of accumulating the energy for later use. For CNGES, this can occur at either a closed volume (such as underground storage or aboveground cylinders) or at a flowing pipeline.
A flowing pipeline differs from other forms of energy storage in that gas is continuously entering and exiting the system at its end points. The amount of storage corresponds to the energy that can be converted to electricity from the inventory of gas accumulated inside the volume of the pipeline between the minimum pressure at the end of a discharge (minimum line pack) and the maximum pressure at the end of a charge (maximum line pack).
The maximum line pack is set at a pressure that is lower than the maximum allowable operating pressure (MAOP) of the pipeline segment. The minimum line pack is set at a value that is higher than the minimum pressure needed to deliver the required flow of gas at the minimum specified end point pressure, considering associated system pressure losses.
Underground or aboveground storage can be connected to the pipeline to incrementally increase storage capacity. This additional storage is typically maintained at a pressure level above the pipeline operating pressure to maximize energy density.
Discharging. Discharging is the process of transforming the stored energy back into electricity. For CNGES, this is accomplished by installing new expander generators at pressure reduction stations, which extract energy from the flow of gas as its pressure reduces. The existing pressure reduction valves would then support management of excess flow or serve as bypasses for maintenance.
Expander generators share a general architecture: an expansion turbine is located at the system inlet and a generator is located at the system outlet. High-pressure gas enters the expansion turbine and is directed, via a nozzle, to an expander wheel. As the gas passes through the wheel, it expands and performs work, causing it to rotate. The wheel is coupled to a shaft. The shaft’s rotational energy is then converted into electricity in the generator. Maintenance cost and leakage rates can be minimized by selecting expanders with best-in-class technologies: bearing, sealing, and generator design directly impact these parameters.
Some expander generators utilize rolling element or fluid film bearings to support the shaft. Neither bearing type may be directly exposed to the gas, because of lubricant contamination risk. Therefore, these bearings require that seals be integrated on the shaft between the expander wheel (and the gas) and the generator (and the bearing lubricant). Dynamic seals like labyrinth or dry gas seals are typically used. Over time, dynamic seals wear: regular inspection and maintenance are required to ensure seal health is preserved and gas leaks are prevented. These activities can be avoided by specifying magnetic bearings in the expander generator.
Magnetic bearings eliminate the need for lubricant and dynamic seals. They do so by levitating the shaft in a magnetic field, which creates frictionless operation for the rotating components of the system. Magnetic bearings are designed to operate continuously for decades and can respond to both variable axial and radial loads, ensuring compatibility with changing operating conditions. The capital cost of this preferred technology is justified by its minimized operational cost and its maximized process uptime.
Other systems utilize inductor generators to convert the gas’s potential and kinetic energies into useable electricity. These systems are rated for low-speed operation, and require the integration of a gearbox between the high-speed rotor and the induction generator. Like dynamic seals, the gearbox represents a point of failure that must be monitored and maintained. System reliability can be improved by instead specifying a permanent magnetic (PM) generator.
PM generators can be integrated directly onto the shaft by affixing magnets to its surface. A wound stator is positioned around the magnetized shaft. As the shaft spins, a rotating magnetic field is created, and voltage is generated in the stator windings. These systems are characterized by high-efficiency operation: PM generators in CNGES service can reach electromagnetic efficiencies as high as 98%. Current is transmitted from the stator to a variable-speed drive through hermetic seals, eliminating the possibility of leakage.
The power output depends on the gas flowrate, temperature, and the pressure differential. The gas flowrate is dependent on the demand of natural gas at the low-pressure end of the pipeline. The pressure differential is controlled by managing the line pack as previously discussed. This arrangement allows the expanders to produce energy at higher capacity factors, with a power output that is maximized during peak demand time. The gas inlet temperature can be controlled using heaters.
Heaters. Heaters are typically required at pressure reduction stations to prevent gas from reaching temperatures below freezing or dewpoint. Additional heating is required after installation of the expanders to compensate for a larger temperature differential or to increase electrical output.
Waste heat can be incorporated and is preferred where available. Where waste heat is unavailable, natural gas fired heaters can be installed.
Controls. The process is coordinated by an integrated control system. The control system allows the operator to program charging/discharging cycles and vary settings based on market signals, operational requirements, or weather forecasts.
Abbott Power Plant Pipeline CNGES Concept
The Abbot Power Plant conceptual study illustrates how CNGES integrates over an existing pipeline that feeds a fossil asset.
Existing Facilities. Abbott Power Plant is owned by UIUC and has a nameplate capacity of 84 MW of electricity. It contains six boilers, two heat recovery steam generators (HRSGs), two gas turbines, and nine steam turbine generators. The three natural gas fired boilers are each capable of producing up to 175,000 lb/hr. The three coal boilers collectively can produce up to 350,000 lb/hr. The two HRSGs work in conjunction with the plant’s two natural gas turbines and generate approximately 40,000 lb/hr from their flue gases. The ductwork between the gas turbine exhaust and the HRSG also is equipped with natural gas–fired duct burners. When these burners are used, the output from the HRSGs increases from 40,000 lb/hr up to 110,000 lb/hr. The nine steam turbines have two exhaust modes: condensing and extraction. In extraction mode, steam is exhausted from the turbine and diverted to the campus system for heating.
UIUC generates additional renewable power from the campus solar farm and has a purchase agreement for wind power. The 21-acre Solar Farm-1 generates 4.68 MW power, while the 54-acre Solar Farm-2 generates 12.1 MW power. A Solar Farm-3 is being planned. The campus receives 8.6% of the wind-generated electricity from the Rail Splitter Wind Farm (about 25,000 MWh annually). Abbott Power Plant’s CHP generation is required to achieve high ramp rates and high turndown to offset the increasing renewable energy mandates of the university’s Illinois Climate Action Plan (iCAP).
The pipeline that supplies natural gas to Abbott Power Plant is a lateral configuration that starts at Kinder Morgan’s Natural Gas Pipeline Co. of America LLC (NGPL) pipeline meter station, north of Monticello, Illinois, at 700 psig (858 psig maximum operating pressure) and continues to an existing pressure regulation station at Curtis Road, Champaign, Illinois, where pressure is reduced to 400 psig. This pipeline segment is operated by UIUC and is eight inches in diameter and approximately 19 miles in length.
A second segment starts at the Curtis Road pressure reduction station and runs to a gas regulator yard at Abbott Power Plant, where a portion of the gas is sent to the existing gas turbine generators at 400 psig, and another portion is heated, odorized, and reduced to 30 psig for distribution to the boilers and campus buildings. This UIUC operated segment is 10 inches in diameter, approximately 2.7 miles long, and has a maximum operating pressure of 618 psig.
Study Goal. The overall goal of the conceptual (Phase I) study performed by ISTC was to integrate an energy storage system of at least 10 MWh based on CNGES technology with the Abbott Power Plant. The project team determined the optimum locations for the CNGES system components, their utility requirements, interconnection with the existing facilities, permitting and regulatory considerations, and technical requirements for construction. Capital and operation costs were estimated and a technoeconomic assessment of the project was made, along with an assessment of the technology gaps and other aspects needed for commercial implementation.
CNGES Integration with the Existing Facilities. The CNGES system will integrate with the existing facilities by utilizing the roughly 22 miles of natural gas pipeline feeding Abbott Power Plant for storing natural gas at high pressure during off-peak demand periods. It will release the pressure of the said gas to recover electricity at the two pressure reduction stations. The model involves two subsystems, one for each pressure level of the pipeline, as shown in Figure 2.
![]() |
2. This Google Maps layout shows the route of the natural gas pipeline and the two subsystems that are part of the compressed natural gas energy storage (CNGES) system. Courtesy: UIUC |
The first subsystem (700 psig) will run from the metering station north of Monticello, Illinois (site A), to the pressure reducing station near the intersection of the railroad and Curtis Road in Champaign, Illinois (site B). The line pack of the 19-mile pipeline section will be controlled by a new control valve on site A that will increase, maintain, or decrease the downstream pressure by adjusting the flowrate of gas supplied from the Kinder Morgan NGPL pipeline. Compression is not required at this point because the pressure originates from the transmission pipeline system.
The energy of the gas will be converted back to electricity at newly installed expander generators to be located on site B, as shown in Figure 3. Given that site B does not have an existing waste heat source, an additional water-bath heater will be installed in series with the existing unit.
![]() |
3. A 3D rendering of the Curtis Road pressure reduction station is shown here. Courtesy: UIUC |
The second subsystem (400 psig) will span from site B to the pressure regulator yard located at Abbott Power Plant (site C). The line pack of the approximately 2.7-mile pipeline will be controlled by the site B expander inlet flow control valves, which will adjust the flowrate of gas through the expanders. New expanders will be located at site C, as shown in Figure 4, to recover the energy and generate electricity that will connect to an existing switchgear. Additional heating of the gas will be achieved with a heat exchanger that will use excess heat from the CHP plant.
![]() |
4. A 3D rendering of the Abbott Power Plant gas regulator yard is shown here. Courtesy: UIUC |
In total, the CNGES system will have a nameplate capacity of approximately 1.1 MW and will be capable of generating 17 MWh over a 24-hour cycle. The storage capacity within the maximum and minimum line packs, at the CHP plant combustion turbine heat rate, is 91 MWh, for a total integrated energy storage capacity of 108 MWh, capable of supplying up to three hours of duration at the total combustion turbine nameplate capacity.
The predicted CNGES system performance is shown in Figure 5, which illustrates the line pack, inventory of gas, and the expander power outputs over a 24-hour period in minimum monthly average temperature (January) and maximum monthly average temperature (July) conditions. These curves assume six-hour charging and discharging periods, with six-hour intervals in between, based on the current power plant natural gas and electrical demand profiles. The CNGES system will operate in load-following mode.
![]() |
5. The performance curves for the CNGES system are shown here. Courtesy UIUC |
The projected capital cost estimate (total owner’s cost) and levelized cost of electricity (LCOE) were estimated for the CNGES system using National Energy Technology Laboratory (NETL) guidelines for either a standalone system or a system integrated with an existing fossil asset. These costs were estimated for the Abbott Power Plant project, as well as for a generic project of similar characteristics but scaled up ten-fold. The results are shown in Table 1.
![]() |
Table 1. Projected capital costs (CAPEX) and levelized cost of electricity (LCOE) are shown here. Source: UIUC |
From an environmental perspective, the system reduces net emissions by displacing grid imports. The calculated net emissions that would be avoided by installing the CNGES system are shown in Table 2.
![]() |
Table 2. Estimates of net emissions avoided are shown here. Source: UIUC |
The CNGES system capacity can be modularly increased by installing aboveground cylinders and compression on site B to store a larger inventory of natural gas at a higher pressure. When augmenting this inventory, the system can achieve a total capacity of 387 MWh, or sufficient for a duration of 12 hours. These aboveground storage facilities are not covered in this article.
Evaluating CNGES Potential at Existing Pipelines
The feasibility of deploying CNGES at a pipeline system needs to be addressed site by site because the capital and LCOE vary greatly depending on system characteristics. Some of the variables that impact project economics include:
- ■ Pipeline physical construction data and operating specifications.
- ■ Natural gas composition, specifications, and demand profiles.
- ■ Compressor station configuration and operation regime.
- ■ Pressure reduction station configuration, downstream delivery pressure, and minimum design temperature.
- ■ Electricity and natural gas market pricing.
- ■ Regulatory factors.
In general, systems most favorable to the deployment of CNGES technology include several of the following characteristics:
- ■ Compression Stations. Electrically driven or hybrid electrical/combustion-driven compressors, close to renewable energy sources and surplus capacity, are optimal. Sites with clean peaking standards may benefit from shifting compression load to clean system peaks to capture the incentives.
- ■ Pipelines. Pipelines operating at transmission-level pressures (the higher, the better), with longer lengths and larger diameters (higher volume), with a wide pressure margin between the maximum allowable operating pressure and the minimum pressure required to deliver natural gas.
- ■ Pressure Reduction Stations. Large consumers of natural gas, such as power plants or industrial customers, that also have electrical systems capable of receiving the expander generator output, are ideal. Customers whose natural gas demand profile is steadier throughout the day are also favorable, as they allow the expander generators to operate at higher capacity factors. Locations where natural gas demand correlates with the grid’s electrical demand (such as load-following plants) are preferable for coordination of charging and discharging cycles.
- ■ Price Dynamics. Large price spreads between peak and off-peak energy pricing are most desirable.
Systems that do not have these attributes tend to be less favorable for deployment of CNGES, especially where demand for natural gas is intermittent, flowrates are low, pressure differentials are small, or where new compression and storage need to be built.
An Innovative Solution Leveraging Existing Resources
CNGES combines energy efficiency, energy storage, and natural gas storage. It is most suitable for high-power, long-duration applications where the solution can be cost-effectively integrated with existing gas transportation and distribution networks. The Abbott Power Plant demonstration shows how CNGES can be integrated with an existing natural gas pipeline servicing a fossil asset to provide technical, economic, and environmental benefits to a grid that is receiving an increased share of renewable energy.
The natural gas infrastructure in the U.S. presents an opportunity for widespread, fast deployment of energy storage, but a thorough technoeconomic assessment needs to be performed to select sites with the most favorable conditions. The CGES concept is applicable to new clean fuels networks, to an existing natural gas network with future upgrades to transport clean fuels, or to any form of compressible gas, including future systems that transport and store carbon dioxide. In combination with other sustainable technologies, CGES can become another tool to reduce carbon emissions.
Acknowledgement: This material is based upon work supported by the Department of Energy’s Fossil Energy Program under Award Number(s) DE-FE0032018. Further acknowledgement to the UIUC Facilities and Services staff for providing support and data for the study.
Disclaimer: This report was prepared as an account of work sponsored by an agency of the United States Government. Neither the United States Government nor any agency thereof, nor any of their employees, makes any warranty, express or implied, or assumes any legal liability or responsibility for the accuracy, completeness, or usefulness of any information, apparatus, product, or process disclosed, or represents that its use would not infringe privately owned rights. Reference herein to any specific commercial product, process, or service by trade name, trademark, manufacturer, or otherwise does not necessarily constitute or imply its endorsement, recommendation, or favoring by the United States Government or any agency thereof. The views and opinions of authors expressed herein do not necessarily state or reflect those of the United States Government or any agency thereof.
—Sebastiano Giardinella is a project engineer at the Prairie Research Institute (PRI), University of Illinois at Urbana-Champaign (UIUC). The following individuals contributed to this article: Kevin O’Brien, Leslie Gioja, Jim Dexter, Scott Prausse, Ryan Larimore, and Laura Barnes, all from PRI, UIUC; Michael Larson and Robert Roman of Abbott Power Plant, UIUC; Alberto Baumeister of Ecotek Engineering USA LLC; Ramon Diaz of Ecotek Investments Inc.; Richard Callahan of Enerfex Inc.; Daryl-Lynn Roberts of Visage Energy Corp.; and Jeff Earl of Sapphire Technologies Inc.
The post Low-Cost Long-Duration Energy Storage at a Natural Gas Pipeline appeared first on POWER Magazine.