The POWER Interview: What Is a Digital Twin?
Credit to Author: Aaron Larson| Date: Mon, 27 Jan 2020 14:59:48 +0000
The post The POWER Interview: What Is a Digital Twin? appeared first on POWER Magazine.
The term “digital twin” is used frequently by tech-savvy power industry professionals, but what does it really mean?
To get an insider’s perspective, POWER posed the question to Akshay Patwal, strategic business manager with Siemens Energy. Patwal leads the development and commercialization of digital business transformation projects, using big data platforms and analytics, to create data-driven services. He has been pioneering the building of digitalization and big data-based framework by developing and implementing company-wide platforms, systems, and business processes to maximize the value of enterprise data, driving performance improvement, cost reduction, and revenue generation. He is an expert and thought-leader on data management, data analytics, and visualization technologies in the energy industry, so he obviously has a wealth of knowledge on the subject.
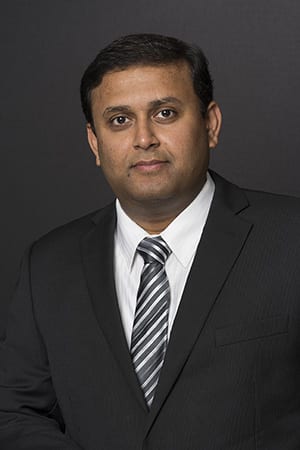
Akshay Patwal is strategic business manager with Siemens Energy. Courtesy: Siemens
POWER: What is a digital twin?
Patwal: In power generation, digital twin refers to the mapping of the physical asset models in a digital platform, where a virtual digital replica model is created. This is created using the asset-related data obtained from various sources, combined with deep domain knowledge about the asset. This virtual model is built using information from massive amounts of design, manufacturing, inspection, repair, sensor, and operational data.
A lot of high-fidelity computational physics-based and analytics-based models are housed in the virtual model to analyze and forecast health and performance of operating assets over their lifetime. This allows the operator to understand operations of the asset and prevent unexpected failures. The technology in the twin informs about the asset behavior and allows the user to take necessary actions. Based on this knowledge, the maintenance of the asset can also be optimized. This results in the asset being kept in the optimal level of operation, rather than performing random, uncertain and reactive maintenance.
The other key aspect to a digital twin is the usage of the right software to analyze and visualize data, which allows operators to manipulate digital asset conditions for scenario planning without interfering with the operation of the physical asset. Some of the key goals of the digital twin are cost savings, revenue increase, reduced outages, improved operations, and market dynamics management.
The digital twin performs asset life estimates, detects behavior anomalies, and calculates thermal efficiency to ensure that the operations and maintenance processes are optimized across the power plant. It also allows cross collaboration with other industries, which have similar dynamics as the power generation industry.
POWER: What other benefits has digital technology delivered to the power industry?
Patwal: Digital technologies are transforming the power generation industry, providing new insights into power plant planning, operations and maintenance, and uncovering new avenues to boost system performance, and increase equipment availability and reliability. Traditionally, most of the data generated within the power industry was limited to remote monitoring and diagnostic services, where it was analyzed to monitor turbine operations. But with the advent of newer data sources and data management approaches—complimented by analytical capabilities—newer opportunities are being envisioned for greater understanding of customers’ business needs and power plant equipment dynamics.
A lot of new opportunities for utilization of data have emerged, resulting in novel customer business models tailored to satisfy their specific requirements around operational flexibility, maintenance optimization, and enhanced planning. The digital approach goes beyond simply gathering data or offering a software program, by integrating structured and unstructured data from different sources, and performing insight-driven analytics on it to provide recommendations to improve plant performance and optimize maintenance.
Utilities need to realize that they must embrace digitalization to streamline their businesses for efficiency and sustainability, while improving customer experience. This will result in critical data-driven business decision-making to understand current and future market trends, and develop strategies to manage risks and costs across all divisions, while maximizing asset utilization. With the growth of decentralized and renewable energy sources, customers desire increased flexibility and smarter solutions to generate data-driven actions. To be competitive in uncertain markets and save money, companies need to look at varied scenarios by analyzing real-time data streams generated by power plant operations, planning, and maintenance.
POWER: How is technology changing power plant operation today?
Patwal: Operational Technology (OT), which is the network of power plant systems involved in power generation, and Information Technology (IT), which is the network of communication, data management, and data analysis systems, are integrated to create a digital landscape to obtain significant gains in efficiency, speed, and effective control in power plants. This enables companies to centralize important aspects of system and process management, and outsource desired services.
Most of the offerings in the digital landscape in power generation have been around the following key areas:
- Increasing Availability. This approach guides power plant operators to optimize equipment inspections, regulate periodic maintenance activities, and optimize condition-based maintenance with the balancing of operations and maintenance activities with reliability and inventory management.
- Performance Improvement. This solution manages plant operations in terms of flexibility and improves performance to enhance profitability in the ever-changing market.
- Remote Field Support. This digital approach and virtualization allow the monitoring and diagnostics of power plant assets to have early detection of the anomalies and impending damage to them.
- Risk and Compliance. The integration of the OT and IT networks has placed greater stress on preventing cyberattacks on power plants. The cybersecurity umbrella over the digital landscape monitors networks for growing cyberattacks and reduces risk while ensuring compliance with industry standards.
- Fleet Management. This system of monitoring and diagnostics offers full transparency across machine, plant, and fleet level, and provides asset diagnostics, performance monitoring, and operations optimization to create new avenues for utilities to manage and market their assets.
POWER: How will future power plants differ from today?
Patwal: The race to the future power plant, which is quite often called “Power Plant of the Future 4.0,” is in line with the Industrial Revolution 4.0. It has led to the introduction of Internet of Things (IoT) in the power generation industry. IoT is the network of interconnected devices or things embedded with sensors, network connectivity, data management systems, and analytics engines to collect, manage, and analyze data to generate actionable resources.
This concept has been further extended to industrial scenarios and is often referred to as Industrial Internet of Things (IIoT). While both IIoT and IoT have the same main character, that is, availability of intelligent and connected devices, in most cases, IoT is used in the consumer domain and IIoT is prevalent in the industrial realm.
The Power Plant of the Future 4.0 goals are pushing the territories of power plant operations and maintenance toward an autonomous scenario to reduce costs and increase revenue. The comprehensive transformation of electric power markets is due to the transition from fossil generation to renewables and distributed generation. There has been decentralization in power generation units, resulting in complication in operations.
IIoT plays a key role in the integration of OT and IT networks, and lays out a comprehensive sensor network to generate operational and system data, provides a data management module to manage data, and an analytical backbone to analyze data to discover new insights, provide prescriptive recommendations, and take necessary actions. It intends to provide the following capabilities in power generation:
- Autonomous Power Plants. Power plant operations, asset maintenance, and planning are done by analyzing the data generated across the board and taking necessary actions with limited human interference.
- Comprehensive Fleet Management. Sensor data across the whole fleet and plant is monitored, and data is analyzed to perform asset diagnostics, performance monitoring, and operations optimization.
- Performance Improvement. Analysis of performance data provided by sensors provides recommendations and actions to be done to ensure that the performance of power plant assets is maintained at the desired level within market constraints.
- Cybersecurity. The cyber data from IIoT provides an automated way for early detection of cyberattacks on the IT and OT networks, and prevents any further damage.
- Complete Remote Operability. The decentralization of power sources has necessitated distributed and remote control of power plant operations. The introduction of mobile remote controlling is playing a major role in replacing the manual control operations.
—Aaron Larson is POWER’s executive editor (@AaronL_Power, @POWERmagazine).
The post The POWER Interview: What Is a Digital Twin? appeared first on POWER Magazine.